Understanding Titanium Fasteners Manufacturers and Their Impact on Industry
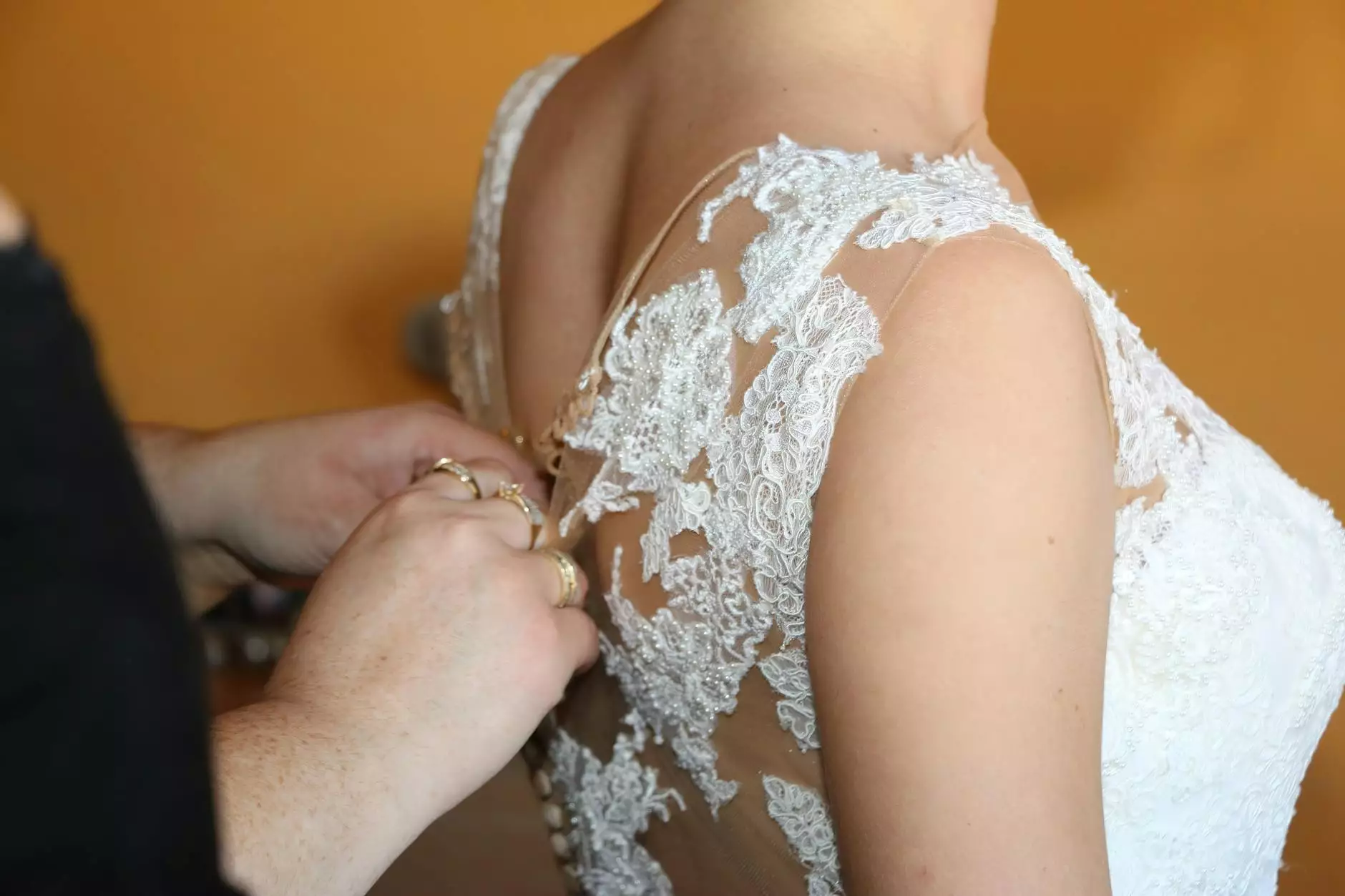
Titanium fasteners are at the forefront of modern manufacturing and construction due to their exceptional strength-to-weight ratio, corrosion resistance, and biocompatibility. As titanium fasteners manufacturers continue to innovate, they play an increasingly vital role in various sectors, especially among general contractors who rely on durable and efficient hardware solutions. This article delves deep into the world of titanium fasteners, exploring their manufacturing processes, benefits, and applications, as well as the pivotal role they play in enhancing construction projects.
What Are Titanium Fasteners?
Titanium fasteners are specialized hardware components made from titanium or titanium alloys. These fasteners are produced in various shapes and sizes, serving functions similar to those of traditional fasteners, such as bolts, screws, nuts, and washers. Their unique properties make them highly sought after in industries where strength, durability, and low weight are critical.
The Importance of Choosing the Right Material
When it comes to construction and manufacturing, the choice of fasteners is crucial. Traditional materials like steel or aluminum can offer certain benefits but fall short in specific applications. Titanium, as a material, brings forward several advantages:
- Strength: Titanium has an incredibly high tensile strength, making it ideal for demanding applications.
- Corrosion Resistance: It resists corrosion better than many metals, which is vital in harsh environments.
- Lightweight: Being significantly lighter than steel, it reduces the overall weight of structures without compromising strength.
- Biocompatibility: Titanium is non-toxic and not rejected by the human body, making it suitable for medical applications.
The Manufacturing Process of Titanium Fasteners
The production of titanium fasteners involves several complex steps, ensuring that the final product meets high standards of quality and performance. Understanding this process is essential for general contractors who want to source reliable hardware for their projects.
1. Material Selection
The manufacturing process begins with the careful selection of titanium or titanium alloy. The most common alloys used in fasteners include Ti-6Al-4V (Grade 5) and Ti-3Al-2.5V, which offer an excellent balance of strength, ductility, and weldability.
2. Forming Techniques
Once the material is selected, titanium powder or bars are subjected to forming techniques such as:
- Forging: A method that involves shaping the metal under heat and pressure, enhancing its grain structure.
- Machining: Involves cutting, turning, or milling to achieve precise dimensions and tolerances.
- Cold Heading: A process that deforms the material at room temperature to form heads or shapes, minimizing waste.
3. Surface Treatment
Surface treatment is critical in enhancing the corrosion resistance and aesthetic appeal of titanium fasteners. Common treatments include:
- Anodizing: Creates a protective oxide layer that adds corrosion resistance and can modify the color of the fasteners.
- Passivation: Involves treating the surface to remove contaminants and enhance corrosion resistance further.
Applications of Titanium Fasteners in the Construction Industry
Titanium fasteners are versatile and find applications across a wide range of sectors. Here are some key areas where they are particularly beneficial:
Aerospace Industry
In the aerospace sector, weight and strength are paramount. Titanium fasteners are used for critical components in aircraft, reducing overall mass while maintaining safety and performance standards.
Marine Applications
Due to their corrosion resistance, titanium fasteners are ideal for marine construction and equipment, including boats and offshore platforms. They withstand harsh salty environments, ensuring longevity.
Medical Sector
In medical applications, titanium fasteners are used for implants and surgical devices because of their biocompatibility. They do not react adversely with body tissues, making them safe for long-term use.
Automotive Industry
The automotive industry uses titanium fasteners to reduce vehicle weight, thereby enhancing fuel efficiency. They are employed in high-performance vehicles and motorsports, where every gram counts.
Construction and Structural Applications
For general contractors, titanium fasteners are becoming a preferred choice in construction, especially for structures requiring high durability in harsh environments. Their resistance to environmental degradation ensures that buildings remain safe and aesthetically pleasing for longer periods.
Advantages of Partnering with Titanium Fasteners Manufacturers
Working directly with titanium fasteners manufacturers provides numerous advantages for general contractors. Here are key benefits:
1. Customization
Manufacturers often offer customized solutions tailored to specific project requirements. This means that general contractors can source fasteners in unique sizes, shapes, and finishes, ensuring compatibility with their designs.
2. Quality Assurance
Reputable manufacturers implement rigorous quality control measures throughout the production process, ensuring that every batch of fasteners meets industry standards for performance and safety. This reliability is crucial for contractors who want to avoid costly mistakes.
3. Technical Support
Many manufacturers provide valuable technical guidance and support, helping contractors choose the right products for their projects. This expertise can save time and resources by preventing selection errors.
4. Competitive Pricing
By establishing a direct relationship with fastener manufacturers, contractors can often negotiate better pricing and bulk order discounts, reducing the overall cost of projects.
Environmental Considerations in Titanium Manufacturing
As industries strive to become more sustainable, titanium fasteners manufacturers are adopting greener manufacturing practices. Here are some key initiatives:
1. Recycling Titanium
Titanium can be recycled without losing its properties, and many manufacturers are implementing recycling programs to minimize waste.
2. Energy-Efficient Processes
Innovations in manufacturing techniques are leading to reduced energy consumption, making the production of titanium fasteners more eco-friendly.
3. Lifecycle Considerations
Manufacturers are increasingly focusing on the entire lifecycle of products, from production to disposal, aiming to minimize environmental impact at every stage.
Conclusion
In conclusion, as the demand for high-performance materials in the construction and manufacturing sectors continues to grow, titanium fasteners manufacturers are poised to play a crucial role. By understanding the benefits and applications of titanium fasteners, general contractors can make informed decisions that enhance their project outcomes. The unique properties of titanium not only contribute to structural integrity and longevity but also reflect a commitment to innovation and sustainability in modern construction practices. As you explore options for your next project, consider partnering with reputable titanium fasteners manufacturers to unlock the advantages that titanium brings to the table.
For more information about titanium fasteners and to connect with experienced manufacturers, visit titaniumbolts.com.