Etchant for Stainless Steel 304 - The Ultimate Guide
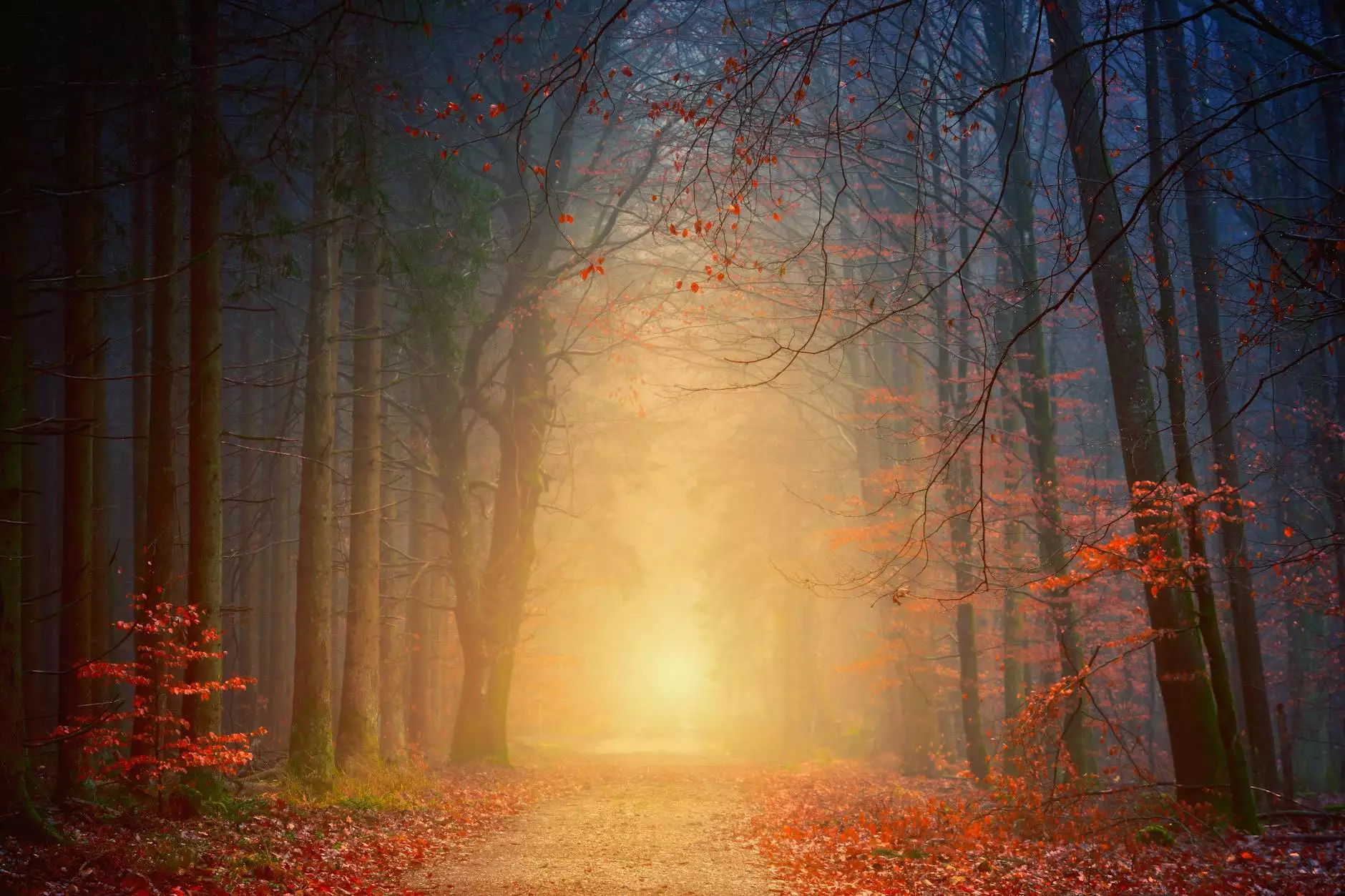
Understanding Stainless Steel 304
Stainless Steel 304 is a widely used alloy known for its remarkable corrosion resistance and durability. This material comprises around 18% chromium and 8% nickel, which contributes to its excellent mechanical properties and its ability to withstand extreme environments. In industries ranging from aerospace to food processing, stainless steel 304 is the preferred choice due to its versatility.
What is an Etchant?
An etchant is a chemical solution that selectively removes material from a substrate, primarily utilized in metalworking and manufacturing processes. When applied to metals like stainless steel, etchants create controlled surface patterns and designs by selectively corroding the surface, which can enhance both aesthetic appeal and functional properties.
The Importance of Etchant for Stainless Steel 304
Using an appropriate etchant for stainless steel 304 is crucial for achieving desired surface finishes and patterns. The benefits of using a dedicated etchant include:
- Enhanced Surface Finish: Achieve smooth, uniform textures that improve both appearance and functionality.
- Increased Adhesion: Prepare the metal surface for painting or coating applications by creating a micro-textured finish.
- Detailed Designs: Make intricate designs for artistic projects, signage, and decorative elements.
- Efficiency: Streamline production processes by effectively preparing surfaces for further processing.
Types of Etchants for Stainless Steel 304
Selecting the right type of etchant is essential for effective results. Here are the most common types of etchants used for stainless steel 304:
- Ferric Chloride: A popular choice for etching stainless steel, effective in removing metal and providing a clean finish.
- Hydrochloric Acid: Often used in combination with other acids to enhance etching power.
- Hydrogen Peroxide and Hydrochloric Acid Mixture: This mixture is effective for creating detailed etching patterns.
- Citric Acid-Based Etchants: Eco-friendly options that are less aggressive but still effective.
Application Process for Etching Stainless Steel 304
The etching process can be broken down into several critical steps to ensure effective and precise results:
1. Surface Preparation
Begin by cleaning the stainless steel surface to remove any dirt, oils, or contaminants. This step is vital as any residue can impact the etching process and the final outcome.
2. Designing the Etch
Utilize software or manual techniques to design the etching pattern. Ensure that the design is appropriately sized and matches the intended use of the product.
3. Applying the Etchant
Carefully apply the etchant for stainless steel 304 using a brush, spray, or dip method, depending on the complexity of the design. Allow the etchant to work for the appropriate amount of time, usually ranging from a few seconds to several minutes, depending on the desired depth of the etch.
4. Rinsing and Neutralizing
Once the desired etch is achieved, rinse the stainless steel thoroughly with water to stop the etching process. It may also be necessary to apply a neutralizing solution to ensure all etchant is removed.
5. Finishing Touches
After rinsing, the surface can be dried, polished, or further coated as needed for the final application.
Safety Precautions When Using Etchants
Working with chemical etchants requires strict adherence to safety protocols. Here are important safety precautions to keep in mind:
- Personal Protective Equipment (PPE): Always wear gloves, goggles, and protective clothing to prevent skin and eye contact.
- Proper Ventilation: Conduct etching in a well-ventilated area to avoid inhaling fumes.
- Storage: Store etching chemicals safely, away from heat sources and in clearly labeled containers.
- Emergency Preparedness: Have access to a safety shower and eyewash station, and know the proper procedures for handling spills and injuries.
Benefits of Using Etchants
Engaging in the etching process for stainless steel 304 provides several advantages:
Enhanced Aesthetics
Custom etching can turn ordinary stainless steel into unique pieces of art or branding material, allowing businesses to stand out in a competitive marketplace.
Functional Improvements
Etching can improve the surface properties of stainless steel, leading to better adhesion for paints and coatings and improving functionality in applications requiring precision.
Cost-Effective Customization
Compared to other methods of customization, etching is often more cost-effective, particularly for small batch productions or unique one-off designs.
Applications of Etched Stainless Steel 304
The versatility of etching stainless steel 304 opens various potential applications:
- Architectural Elements: Create visually appealing panels, railings, and facades.
- Retail Displays: Custom branding and promotional displays that stand out.
- Art Installations: Artists use etched stainless steel to create captivating artwork.
- Industrial Components: Etched components can improve functionality and enhance performance in various machinery.
Choosing the Right Supplier for Etching Services
When sourcing etching services, especially for stainless steel 304, consider the following criteria:
- Experience: Look for a supplier with a proven track record in metal etching.
- Quality Control: Ensure they adhere to strict quality standards and have processes in place to guarantee consistency.
- Customer Service: A reliable supplier should offer excellent customer support to address questions and concerns.
- Customization Options: Choose a supplier that can accommodate a variety of custom designs and specifications.
- Pricing: Evaluate pricing structures to ensure they align with your budget while maintaining quality.
Conclusion
In conclusion, etchant for stainless steel 304 plays a vital role in the metal fabrication industry by enhancing the aesthetic and functional properties of this widely-used alloy. Understanding the etching process, the types of etchants available, and the safety procedures ensures that both craftsmen and industries can benefit from the art of etching. As the demand for customized and functional metal components grows, mastering the etching process will undoubtedly provide businesses with a competitive edge in their respective markets.